Production Delays Are a Thing of the Past with Expert Gasket & Seal Solution
Downtime and production delays are not only stressful, but can cost manufacturing facilities thousands of dollars if not handled properly. When a chemical additives producer was experiencing constant production delays due to pump and seal failure, they reached out to Expert Gasket & Seal for solutions.
Upon investigating the issue, it became clear that many of the issues the customer was facing at their facility were compounded by the fact that they had multiple pumps and mixers hooked up to a single recirculating gear pump for their barrier fluid protection. One specific pump was a constant source of failure. Additionally, the “press” pump was seeing higher pressure than the balance of the group, due to back pressure buildup from a filter press getting clogged and overcoming the seal/stuffing box pressure.
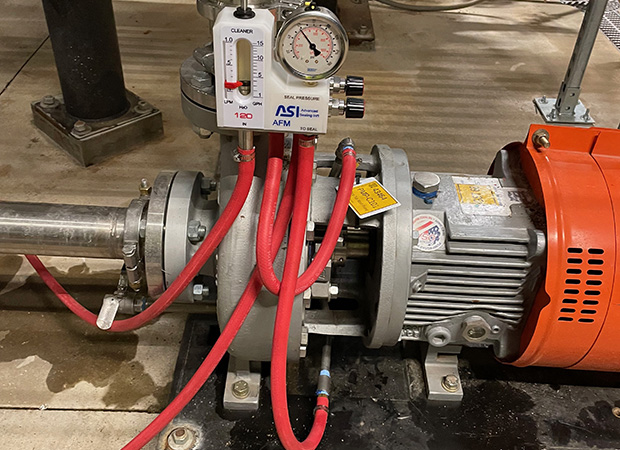
Solution
After Expert Gasket & Seal consulted with an engineering partner, it was determined that the facility needed a double seal with its own ASME stamped seal pot/barrier tank. The pressure on this seal pot would need to be set higher for this single barrier system than what the filter press would create with its back pressure. The tank pressure was set at roughly 65 PSI, which the 595 double pumper cartridge seal can handle easily. The 595 double pumper cartridge seal with the barrier tank is independent of the pump and the pressure associated with the process.
Results
Isolating the 595 double pumper cartridge seal from the others on a “community loop” setup will greatly extend the life of this pump and seal process. By setting this one pump and seal up to its own pressured barrier tank, it can run longer and for extended periods without downtime. This solution should double or even triple the life of the seal and eliminate downtime on a very valuable piece of production equipment for this facility.